在市场境况好的时候,制造企业往往因订单充足、高利润率使物流成本显得不那么重要,企业因而忽视工厂物流成本的节省,优先关注生产扩能或市场拓展。目前受关税壁垒,供应链中断、地缘政治冲突等因素的影响,全球经济增长放缓,贸易不确定性显著增加。而能源价格波动、劳动力成本上升,下游市场需求波动和市场价格战导致企业的成本压力不断增大,对企业生存带来了显著的挑战。
而且,经济不景气时客户对产品价格和货物交付时间更敏感,企业不仅因为低效物流降低了利润率,还导致订单流失,失去市场份额。因此,在原料成本上涨,市场价格竞争越发激烈的背景下,降低工厂物流成本的重要性日益凸显,尤其对像化工企业这样的大宗货物企业至关重要,因其物流成本占总成本比例高达10%-20%,降低物流成本成为提升企业竞争力的关键之一。因此,本文特别以化工企业为例说明优化工厂物流如何降低成本。
一.化工企业工厂物流特点与现状
化工企业工厂物流涵盖原材料接收、生产线配送、半成品/成品存储、库存管理,装卸和发货等环节,工厂物流成本受区域经济差异、劳动力成本变化、技术普及程度,生产模式和规模、自动化水平等因素的影响,特别还受到淡旺季需求的影响。此外,安全要求高,安全成本占物流成本的10%-15%,同时行业利润率又较低(5%-8%)。工厂物流总体现状呈现自动化水平不高、人工依赖较重、季节性挑战大、信息化滞后等问题。
1.物流布局不合理:化工厂生产设备布局固定,难以调整,大多数工厂物流功能区域混乱,交叉迂回搬运多(搬运时间占总物流时间的30%-40%)。
2.仓储空间受限制:多数化工厂仍采用批量存储,淡季库存积压严重,库存周转率很低,库存持有成本占20%-30%。特别是老旧化工厂厂区仓库空间有限,厂区道路两侧经常堆满货物,大多数都在厂外租用仓库。
3.自动化水平不高:物流全信息化自动化企业仅占20%-30%,例如沿海地区大型国企或者外资公司。中小企业或传统制造企业大部分使用人工和有限的自动化设备,导致大部分企业旺季时装卸车辆等待时间长,发货准时率常低于85%-90%。
4.人工作业成本高:由于依赖人工和叉车作业,企业需要雇佣较多工人,人工费用通常占物流成本的30%-50%。不仅工人工资逐年上涨,由于人力短缺旺季还经常招不到人。
二.化工企业厂内物流优化措施
化工企业通常采用大型设备进行连续或批量的流水生产,生产过程高度自动化且设备布局不容易变更。在化工厂的固定布局下,工厂物流优化主要集中在成品下线后的存储,装卸和发货环节,关键是优化功能区域和物流路径、实施自动化,信息化和标准化操作,提高效率并降低成本。
1.调整物流功能区域:在厂房布局和工厂设备不可调整的情况下,可重新调整厂内物流布局,按照生产和物流顺序调整产品在厂区内不同仓库的存储位置,减少搬运距离和时间,设置专用装卸发货区,减少旺季卡车等待时间。
2.设计单向物流动线:结合功能区域调整,识别厂内物流瓶颈和重复路径,设计从生产线到装卸区的单向路线,使物料按单一方向流动,减少人货交叉和拥堵,使产品流转更顺畅高效,提高物流效率并降低成本。
3.提高搬运装卸效率:引入自动化装卸搬运设备(如AGV,输送带、码垛机,装车机等)和信息系统(如WMS、WCS),减少叉车使用和人工干预。,降低人工成本。目标是提高搬运效率,实现单向物流动线,同时消除安全隐患。
4.实施标准包装体系:统一产品的包装和搬运工具规格(如周转托盘、包装袋。桶装等),便于产品通过叉车或输送带的快速搬运和装卸,并减少存储空间需求。使用可回收周转托盘,通过信息化实现货物在厂内的实时跟踪和管理。
5.优化仓储管理模式:在厂内仓储空间不足的情况下,最大化利用垂直空间。在厂区建设部署自动化仓库系统,通过堆垛机和穿梭车提高存储效率。改善库存管理模式,将物料按使用频率分区,优化产品存储,降低库存成本。
三.化工企业厂内物流优化效果
优化工厂物流系统总体上可降低企业物流成本的20%-30%、提高物流效率30%-50%,发货准时率增加至95%-97%。化工厂物流优化的案例表明,物流成本每降低1%,可提升利润率0.2%-0.3%。
案例一:某化肥厂产品主要是50kg包装袋,引入自动输送和机器人码垛机,实施从生产线到装卸区的单向物流动线,通过部署AGV,自动装车机,WMS系统,总物流成本降低18%,工人安全事故减少80%,年节约500万元。旺季发货准时率从85%提升到97%,客户满意度提升,旺季订单续签率增加10%。
案例二:某石化企业生产50kg桶装和袋装液体/粉末化工品,采用自动袋装机和输送带,使用机器人码垛机,引入真空吸吊机,部署自动化立体仓库,空间利用率提升40%,总物流成本降低20%,危险品搬运事故减少90%,年节约600万元。发货准时率从80%提升到95%,客户满意度提升,订单量增长8%。
案例三:某水泥厂采用50kg水泥袋,引入自动输送带和自动码垛机,设置单向通道,部署WMS和AGV,实施5S管理,厂区仓库空间利用率提升30%,总物流成本降低15%,工人安全事故减少70%,年节约400万元。发货准时率从88%提升到96%.客户满意度提升,旺季订单增长5%。
四.消除对优化厂内物流的顾虑
尽管化工企业也认识到优化工厂物流的好处,但是真要实施优化大多数企业仍然存在顾虑,主要是担心可能导致生产中断,投入成本高、回报周期长或效果不显著等。此外,企业可能缺乏专业技术或经验,担心新的模式增加工作负担或不适应。有的企业也担心在实际推进中部门间协同不力、推诿扯皮,导致优化落不了地。这些顾虑都是可以理解的,也很有道理。但是,也不应该成为实施优化的障碍。事实上,无论什么优化方案都不可能是一步到位的,需要制定循序渐进的计划,只要企业看到过程是可控的、收益是可见的、生产是安全的,顾虑自然就会消除。因此,工厂物流优化需要遵循以下原则:
1.采取试点 + 验证 + 扩展步骤,优先选择对核心生产影响最小的环节。
2.制定详细的风险评估和应急预案,出现问题能快速切换回原有模式。
3.每个项目都有清晰的投资回报率(ROI),优先做“低投入、高收益”的项目。
4.尽量改造现有设施,而非推倒重建,用对的方式投资在最划算的地方。
5.不盲目投入硬件,尽量用数字化手段优化物流成本和效率。
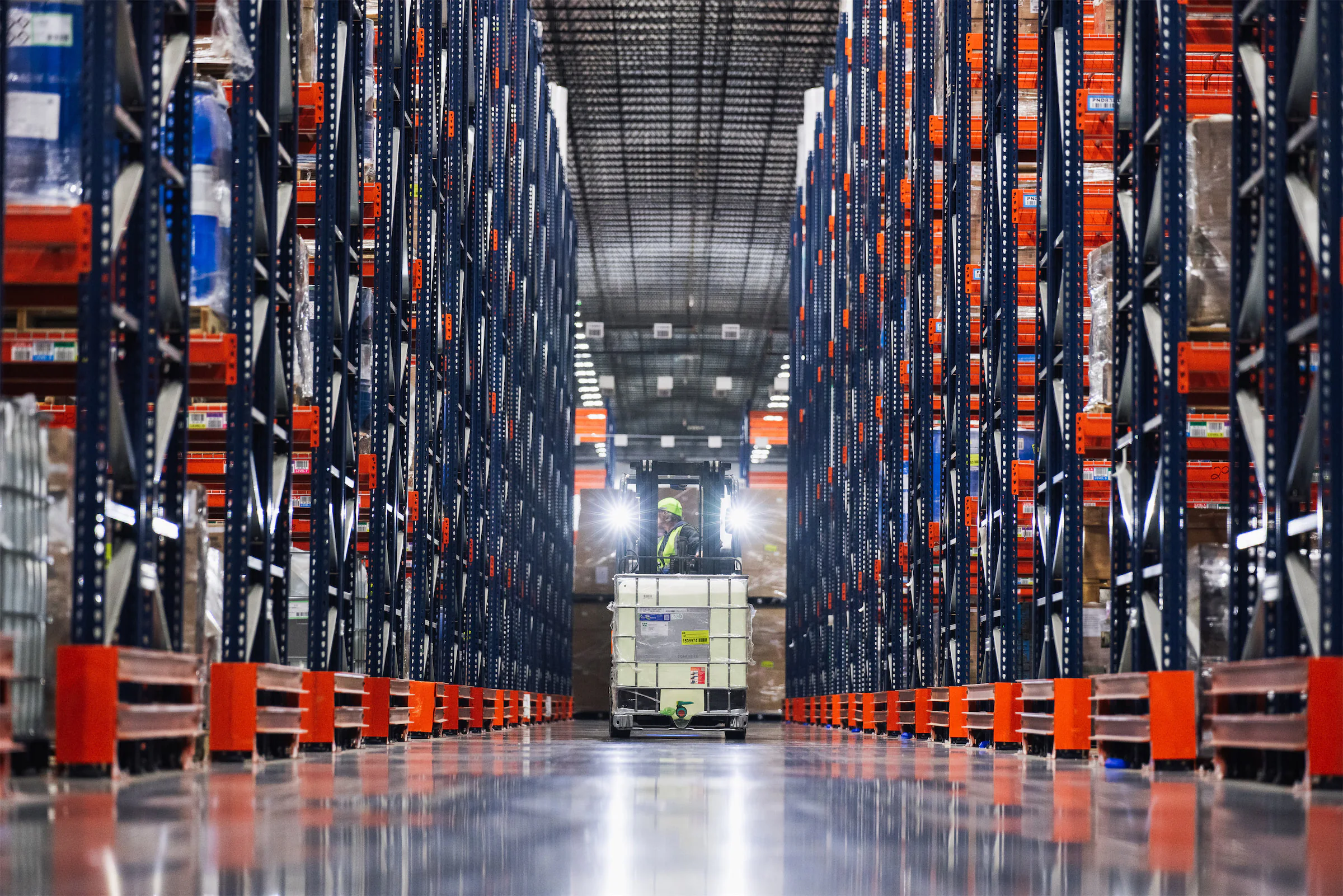